Conveyor Belting 101
What are the Fundamental Building Blocks of a Conveyor Belt?

The Carcass
The carcass is the “heart” of the conveyor belt and is composed of carefully selected raw materials.
Polyester and Nylon
Polyester is primarily used in the warp (lengthwise) for tensile strength, while nylon, more expensive than polyester, is used on the weft (crosswise) to provide flexibility for the belt to trough, track properly and handle smaller pulleys, and impact, rip, and tear resistance for added durability. The quality and grade of these yarns are crucial to the belt’s performance.
There are numerous grades (of variable quality) of polyester and nylon, and therefore, the choice of polyester and nylon yarns has a significant impact on the physical properties of the fabric carcass.
These physical properties are also influenced by how the single yarns are twisted to produce plied yarns, and the quantity of plied yarns used on the warp and weft direction.
RFL Treating
A critical process, where chemicals are carefully selected and heat-set under optimal conditions of temperature, tension and time to achieve superior adhesion. The behavior of chemicals, polyester, and nylon during RFL treatment is crucial, which is why precise material selection is important for optimal performance.
Weave Patterns
The physical properties of the carcass are highly influenced by the weave pattern:
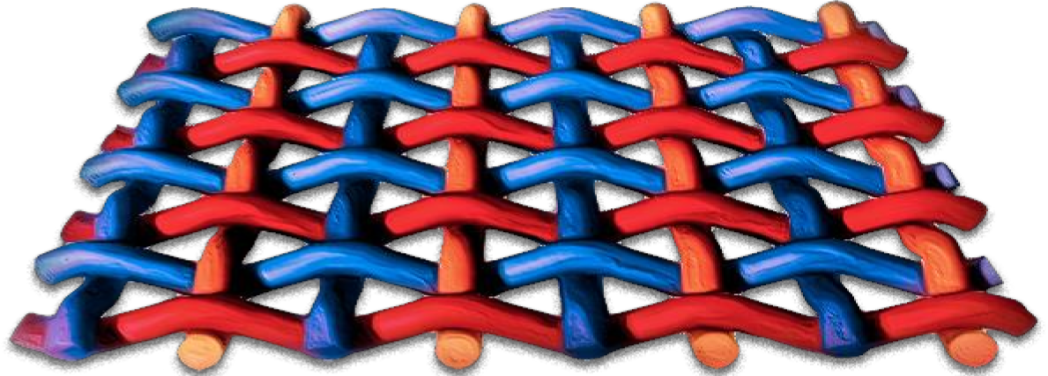
Plain Weave
The traditional pattern used in most belts.
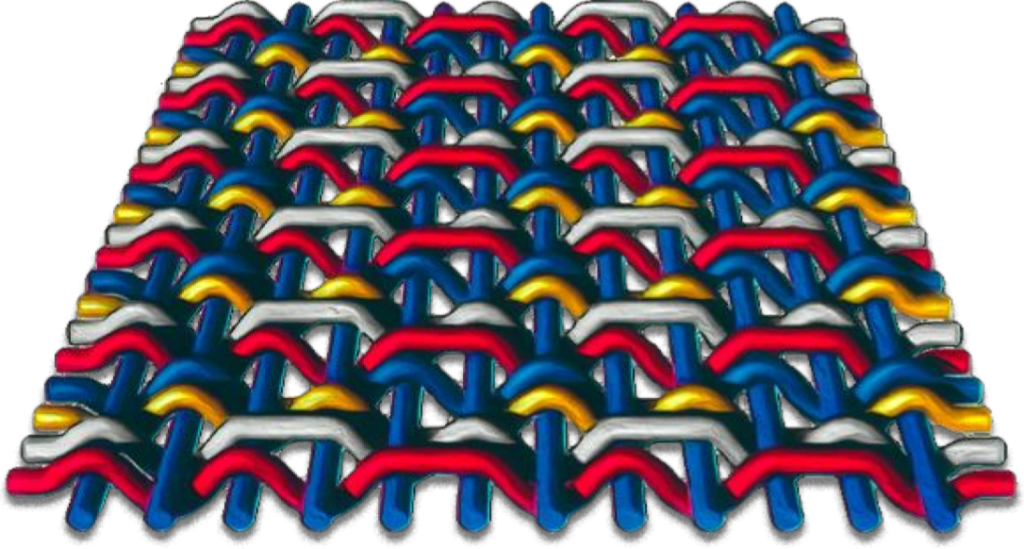
Twill Weave
Used for higher tension applications, offering improved resistance to impact, ripping, and tearing compared to the plain weave pattern.
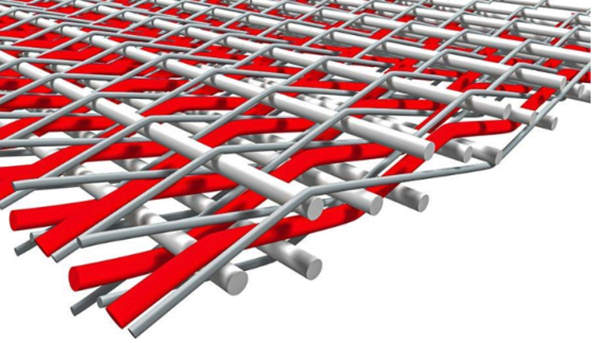
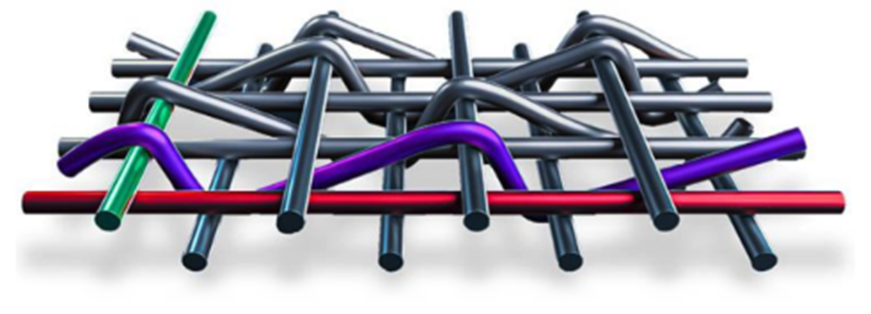
Dual Crimp and Straight Warp
These proprietary weaves by Fenner Dunlop (sold under X Series) provide unparalleled durability and resistance to impact, rip, and tear, setting the standard in conveyor belt performance.
Belts constructed with these weave patterns also deliver superior adhesion, throughability, tracking, load support, and fastener retention, and can handle smaller diameter pulleys.
What are the Key Physical Properties of the Belt Carcass?

While selecting a conveyor belt often begins with operating tension, this property alone is rarely what leads to carcass failure. Instead, the most common failures occur due to ripping or tearing in the warp (lengthwise) direction, or delamination between the plies. Thus, when choosing a belt, it’s crucial to prioritize rip and tear resistance and strong ply adhesion to ensure belt performance and longevity.
The Covers
The composition of conveyor belt covers relies on a blend of carefully selected raw materials:
Polymers
Polymers form the bulk of the cover, with Styrene Butadiene Rubber (SBR) being the most common choice. High-quality covers use carefully selected grades of SBR to enhance abrasion resistance and adhesion, among other physical properties. Conversely, lower-grade SBR compromises these properties, reducing the belt’s longevity. Butadiene and natural rubbers may also be used to further improve resistance to abrasion, cut and gouge. For specialty applications, additional polymers are incorporated to provide resistance to oil, heat, and fire. The quality and formulation of these materials are vital for ensuring the cover’s durability and performance.
Carbon Black
A critical reinforcing agent, carbon black has a significant influence on the abrasion resistance of covers, among other physical properties. With hundreds of grades available, careful selection is crucial to meet the required performance standards.
Anti-Degradants
Essential for the longevity of covers, anti-degradants protect against ozone by forming a protective surface barrier. Low-quality covers often skimp on these, leading to premature aging.
Plasticizers, Oils and Curatives
Used to facilitate processing, these components don’t directly influence the cover’s physical properties but are necessary for proper formulation.
What are the Key Physical Properties of the Cover?

Abrasion resistance is the most critical factor affecting cover longevity, often making it a primary consideration alongside the operating tension of the carcass. However, in some applications, resistance to cut and gouge is more important. The cover’s tensile strength and elongation at break are indicators of its ability to withstand such damage. Delamination between the cover and the carcass plies is another frequent issue, emphasizing the need for high adhesion.
Additionally, covers must resist aging caused by ozone exposure. Ozone exposure can lead to cracking, which exposes the carcass, and reduced tensile strength, and elongation at break, which degrades resistance to cut and gouge.
Therefore, selecting covers with high adhesion, and robust resistance to abrasion, cut, gouge, and the damaging effects of ozone, is essential for maintaining belt performance and longevity.
What Test Methods and Standards Exist to Assess these Physical Properties?

Accredited test methods are available for most of the physical properties discussed earlier. However, in many cases, there is no established standard. Without a standard, a test method is not particularly useful as it lacks a true benchmark for performance and acceptability. In addition, even when standards do exist, they represent only the minimum level of acceptability, rather than measures of true performance.
A notable gap in tests and standards is the absence of methods and benchmarks for rip and tear resistance of the carcass. This absence likely contributes to the widespread availability of conveyor belts with insufficient resistance to these critical failure modes, underscoring the need for careful material selection and adherence to the best design and manufacturing practices.
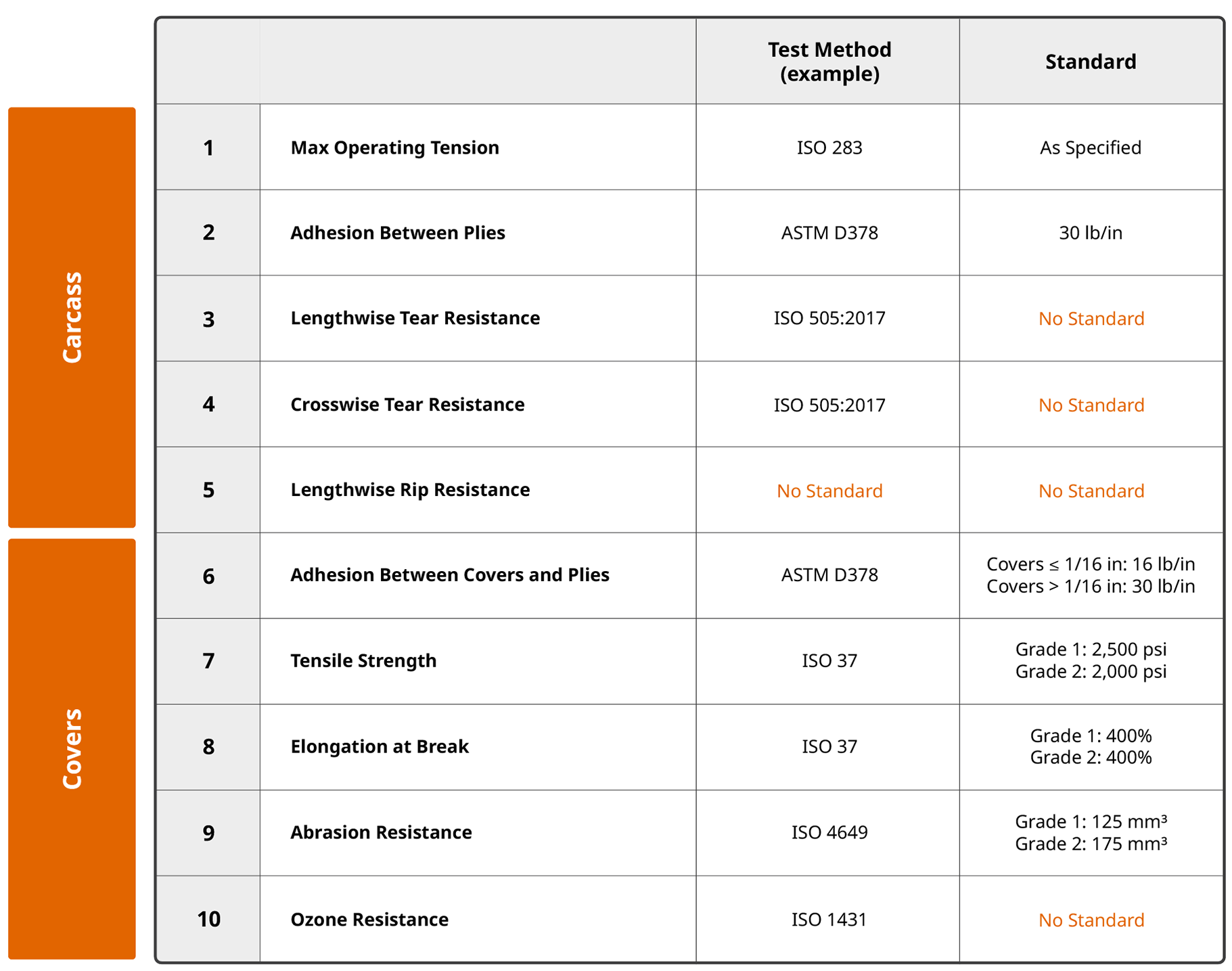
What Common Practices Oversimplify the Belt Selection Process?

Hint: Operating tension and the cover “grade” are only part of the story!
Overemphasis on the Operating Tension
Conveyor belts are often marketed based on operating tension, which relates to the warp (lengthwise direction). Polyester is used in the warp for its strength, but belts rarely fail due to operating tension. Instead, failure is usually related to subpar physical properties on the weft (crosswise direction), where nylon is used. Nylon provides crucial flexibility for troughing, tracking, and handling smaller pulleys. It also adds essential impact, rip, and tear resistance, as well as better fastener retention and load support. However, because nylon is more expensive, low-quality belts minimize its use, compromising overall durability. This is why weft performance is critical but often overlooked in discussions about belt longevity.
Misleading “Grade 1” or “Grade 2” Labels
ARPM standards, commonly used in North America, set minimum requirements for abrasion resistance, among other physical properties. For instance, “Grade 1” covers must have a DIN abrasion value of 125 mm³ or less. However, there is significant variation within this grade. For example, a cover with a DIN abrasion value of 120 mm³ will have a significantly shorter lifespan than one with a DIN of 60 mm³, even though both meet the “Grade 1” classification for abrasion resistance. Low-quality belts typically aim for the bare minimum to cut costs, leading to reduced durability. This is why belt covers are often sold as “Grade 1” or “Grade 2”, even though these and other commonly used general classifications are insufficient to judge the true longevity and performance of a cover.
What is Being Done to Minimize Waste for a Sustainable Future?
Traditionally, conveyor belts were made with multiple fabric plies bonded by layers of rubber. For applications requiring greater resistance to rip, tear, and impact, the common solution was to add more plies and thicker covers. However, this approach is often inefficient and resource heavy.
Fenner Dunlop has taken a more sustainable and efficient path with the X Series. These belts use a single or dual fabric ply design, eliminating the need for extra plies and rubber skims between the plies. This innovation not only conserves resources but also results in a stronger and more durable product.
Additionally, with manufacturing facilities located in the US and Canada, Fenner Dunlop reduces carbon emissions associated with long-distance transportation, further contributing to a sustainable future.
Ready to Get Started?
Contact us today and a member of our team will be happy to discuss your needs and find the right product for your business.